Automated guided vehicles (AGVs) and autonomous mobile robots (AMRs) have revolutionized material handling and similar functions across a number of sectors, including warehousing, automotive, food & beverage, and others. They are boosting productivity, accelerating throughput, and reducing costs—amounting to substantial profitability gains for operations around the world.
Even so, however, the significant benefits currently being enjoyed by many facilities through their AMR/AGV fleets are still only at the tip of the iceberg. There is a lot more potential for productivity, speed, and cost-efficiency benefits just waiting to be captured.
Here’s why: When AGVs, AMRs and similar innovations were first introduced, the best and cheapest power source available at the time, for the most part, were lead-acid batteries, and many robotic OEMs and operators specified them. They were a fine “starter battery technology,” helping AGVs and AMRs deliver many of their promised benefits.
In the years since, however, Li-ion battery technology has emerged and evolved into a superior power source for AGV, AMR, and similar applications. The additional benefits of lithium can be considerable and attainable, with more and more conversion kits and services available, operators can upgrade their fleets at a modest cost and a faster ROI.
A host of profitable benefits
When we showcase the benefits of Li-ion batteries in AGV and AMR fleet applications, the first thing that attracts attention is the vast improvement gained in charging speed and procedures. Whereas lead acid batteries need to work until full discharge and then be charged for upwards of 5 straight hours or more depending on the size of the battery. Li-ion batteries can inherently accommodate “opportunity charging.” That is, no matter what their state of charge, they can be “topped off” for just 10-20 minutes and get a large power gain for hours of extra work and can be fully charged in as little as little as two hours. Some Li-ion batteries can be fully charged in a much shorter time than even that!
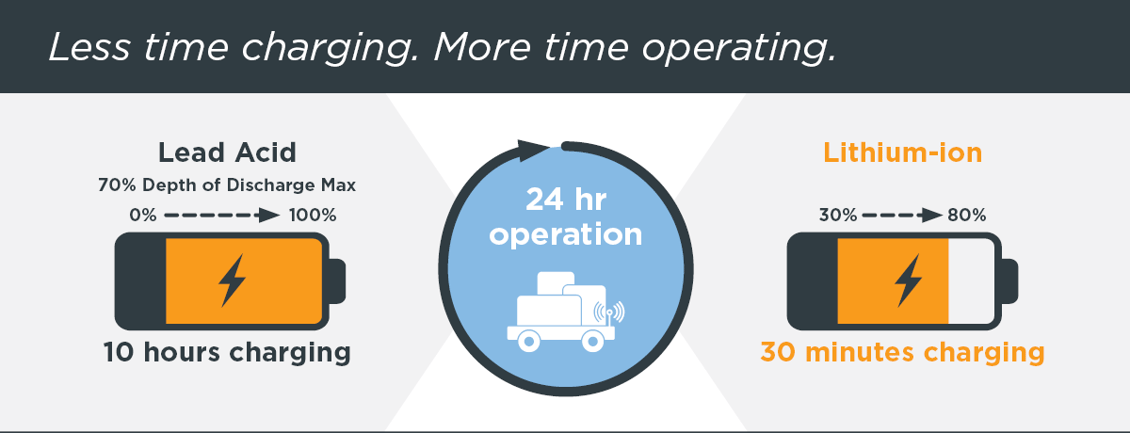
With these improvements in charging, facilities benefit from an increased uptime. After all, what good are robots that can work 24 hours a day if they need to be plugged in and charged for more than 5 hours at a time? With Li-ion batteries, operators can finally reach the true benefit potential of their robot fleets, and get near continuous, non-stop service out of them.
In some applications, OEMs are designing AMRs with wireless charging technology which further enhances efficiency and productivity. AMRs can navigate to their charging stations autonomously or stay charged by connecting with wireless charging pads installed on the floor. Wireless charging is enabled using smart battery technology, such as Lithium-ion batteries, where data communication and charging connectivity is programmed through the battery management system (BMS).
Li-ion batteries also have higher power and energy densities, allowing them to fit in a smaller, more compact footprint. That means operators can work bigger payloads and get more tasks per hour out of their robots—as well as more runtime!
Li-ion batteries also require little or no maintenance as opposed to lead acid batteries, which requires “watering” and other upkeep tasks. They last longer, as they can be charged many more cycles than lead acid batteries. And they work tirelessly in any environment, again, unlike lead acid batteries, which can see large decays in performance in hot and humid warehouse or outdoor conditions, or frigid refrigerated locations.
The use of Li-ion batteries can also open up new opportunities for IoT and data mining benefits. Unlike lead acid batteries which are “dumb” power sources, Li-ion batteries can collect data and communicate with the AGV/AMR as well as outside devices and networks. Opportunities include autonomous self-charging; providing real time temperature, status and health reports; and maintaining ongoing performance data for analytical, process improvement programs.
Last but not least, there’s personnel safety. As you know, an important benefit of any autonomous fleet is that they take the repetitive motion and heavy lifting—resulting in the potential for injury—off of human operators. However, when run on lead acid batteries, this benefit was necessarily accompanied by a new safety threat: lead acid batteries outgas potentially dangerous vapors, especially during charging. This often necessitates creating central charging stations isolated from people—a costly endeavor that also takes up valuable real estate in a facility. With Li-ion batteries, AGVs and AMRs can be charged anywhere there is a standard outlet, with no additional safety concerns.
Wide variety of proven Li-ion batteries available—even customized solutions
Even with all these benefits, we believe that Li-ion technology is just reaching its stride. Unlike lead acid, a mature technology that has likely reached its peak, lithium-ion technology is finding its place in new applications, such as robotics, that can benefit from its high energy density, no maintenance, long life, intelligence, and more.
Inventus Power works with AGV/AMR manufacturers to specify the optimal battery solution for their machines. In fact, we have a broad portfolio of tested, proven, and UL-certified lithium-ion batteries for the robotics industry, including:
In addition, Inventus Power has extensive in-house design and engineering expertise to customize a battery solution for any AGV or AMR development project that will truly optimize performance and operating efficiencies. Contact us today to start a conversation.