Mobile robots will be increasingly common in worksites and industries over the next five years. By 2027, growth in the Automated Guided Vehicles and Autonomous Mobile Robots (AGV and AMR) market is expected to exceed $18 billion. As positions for labor-intensive, repetitive tasks become more difficult to fill, and U.S. unemployment rates remain low at 3.6% as of April 2022, companies will be increasingly receptive to mobile robotic solutions to maintain production and break the logjam.
The benefits of jumpstarting the AGV/AMR development can increase throughput and efficiency while improving workplace safety for a breadth of industries, such as:
- Warehousing
- Automotive assembly
- Lawn and garden
- E-commerce
- Agriculture
- Inventory management
- Delivery (indoors and outdoors)
- Hospitals and clinics
Top challenge OEMs face in scaling to market
However, the biggest challenge for OEMs of mobile robotics is the unique environments and hazards each industry presents. Agricultural machines require materials that can stand up to summer heat all while protecting components against dust and moisture. Warehouse AGV/AMRs can require a specific set of capabilities, along with the ability to function in, say, subzero temperatures in cold storage facilities.
To lower some of these escalating development costs and timelines, identifying opportunities to provide standard solutions in place of highly customized components can help. That’s where the selection of the AGV/AMR's power source comes into play. Each application is different. Working with a battery provider with a reputation for building reliable batteries along with battery management systems that meet and exceed standards in multiple industries can provide one area to streamline development and raise the quality of the product.
Benefits of Li-ion technology in AGV/AMR applications
The type of battery as well as the battery management system can make all the difference in the operation and durability of an AGV/AMR vehicle. Though lithium-ion batteries come at a higher initial price point than lead-acid, the longer lifespan, quicker charging, superior performance, and increased productivity will then make up for the upfront costs. Here’s a look at why lithium-ion technology is the best choice for mobile robots for all the above industries.
Longer run time
Li-ion has a higher usable capacity with a depth of discharge range of 80-100%, allowing it to provide more consistent power. Whereas care should be taken to prevent lead-acid batteries from discharging more than 50% of their capacity or their capacity will be diminished.
Lighter load
Li-ion batteries weigh about 40% less than their lead-acid, allowing the AGV/AMR to operate more efficiently.
Fast, efficient charging minimizes downtime
Lead-acid batteries take up to 10 hours to charge whereas Li-ion can reach full strength in a fraction of that time — sometimes in as little as 15 minutes. Even better, intelligent features in the battery management system can send data to the AGV/AMR software system, enabling it to identify gaps in the workflow so it can spend that downtime in the nearest charger. Whether it gets five minutes or a half hour, brief sessions of opportunity charging add up to longer uptime. Li-ion’s value and impact on productivity couldn’t be clearer.
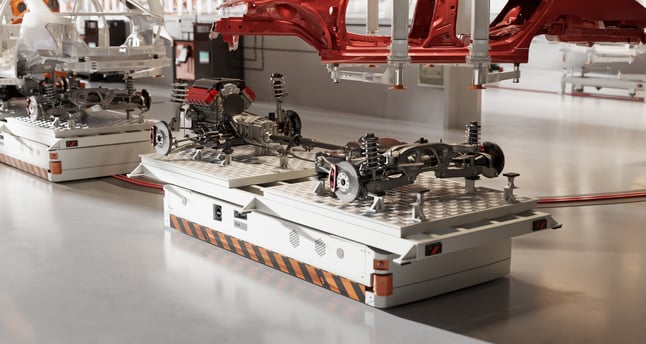
A battery cell doesn’t tolerate extreme temperatures. However, a battery management system can keep Li-ion-powered mobile robots operational even in extreme temperatures. Whether an ag bot is in the field on the hottest days of the year or a warehouse forklift operating in cold storage facilities, a robust temperature management system is designed to actively protect battery cells. In applications like e-commerce and warehousing, a fleet of mobile robotics can be in demand 24/7, elevating the risk of overheating and thermal runaway. That makes it especially important to work with a battery provider that understands the characterization of the battery cells and how to provide proper thermal management.
Intelligence
Lead-acid battery systems have no telematics and no intelligence. It’s simply a block of energy that hooks up to the terminals and senses voltage coming from the battery — providing a rough estimate of the remaining capacity. Lithium-ion is compatible with intelligent telematics systems, so it can transfer real-time data about the battery, how much power it’s drawing, and how much time remains before it’s completely discharged. These smart systems have built-in parameters that prevent AGV/AMR from cutting out in the middle of a job, allowing enough time and distance to reach the nearest available charger.
Inventus PROTRXion: The intelligent battery for intelligent machines
The following will show how Inventus Power’s PROTRXion battery systems provide a safe, durable Li-ion power source for AGV/AMR fleets.
Insights on performance
PROTRXion’s patented battery management system enables useful data on the AGV/AMR performance to be recorded and communicated. Temperature, amp hours of usage, state of charge, state of health, and other important data points allow the operator to track the performance and efficiency of their fleet of mobile robots, so they can optimize job site functionality.
Reliable operation in extreme temperature
The battery management system in PROTRXion batteries is designed to operate in the most extreme environmental conditions, from minus 35 Celsius (when used with an optional heating system) and up to 50 degrees C. Indoors or out, this battery system won’t lose run time or power.
Streamlines development
All of the above qualities come standard in PROTRXion batteries, so they come ready to meet the demands of the most challenging job site: warehousing, manufacturing, agriculture, and more. These robustly designed and rugged battery systems will reduce or even eliminate the need to develop and test custom features. Opting for PROTRXion's toughest industry standards in safety and quality lets OEMs shift resources to other critical areas of the project.
Looking for a long-lasting battery solution to maximize the productivity of your AGV/AMR? Talk to the team at Inventus Power.