The next generation of Li-ion battery technology is continuing to evolve to improve energy density. Consumers have already gotten a glimpse into what that landscape will look like with the introduction of fully electric passenger vehicles (i.e. Tesla, Ford, Hyundai, GM). But commercial vehicles and construction equipment that are fully powered by batteries are paving their way into the market with announced regulations and mandates on emissions and the drive for increased efficiency across many industries.
As the size and power requirements increase for larger, more complex equipment, OEMs need to understand what type of battery they should choose to power their application. The advanced technology offered with high voltage lithium-ion batteries is helping to make electrification happen across many new markets, but certain considerations need to be made depending on the application’s requirements to ensure optimal performance, efficiency, and safety.
What Exactly Does "High Voltage" Mean?
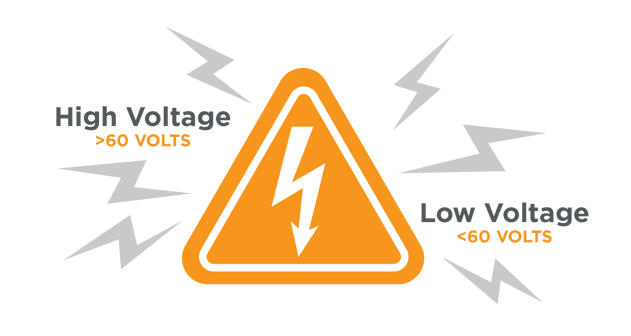
Automotive systems today are already operating at 400 volts with future vehicles being developed at 800 volts. Driving higher levels of efficiency is the goal with a high voltage architecture. Low voltage battery systems (<60V) have to manage more current which requires thicker cabling and more copper to transfer energy back to the system; this increases cost. Efficiency is gained through high-voltage systems because the architecture can support the same amount of power with smaller cabling and less copper.
Higher voltage systems also charge differently than lower voltage systems and can provide faster charging; they are more efficient because less current is required for the same amount of power. Furthermore, by increasing the voltage with the same amount of current, more power can be delivered to the cells through DC-DC fast charging. To further optimize performance, a proper thermal management system (i.e. liquid cooling) can enhance capabilities to deliver more power to the system as well as decrease charge time.
How High Voltage Batteries are Reshaping Industries
High voltage batteries present an array of advantages for the myriad of industries invested in their technology. From off-highway vehicles and construction equipment to low-speed electric vehicles (LSEVs) and energy storage applications, let’s explore the ways high voltage batteries are pushing these industries forward.
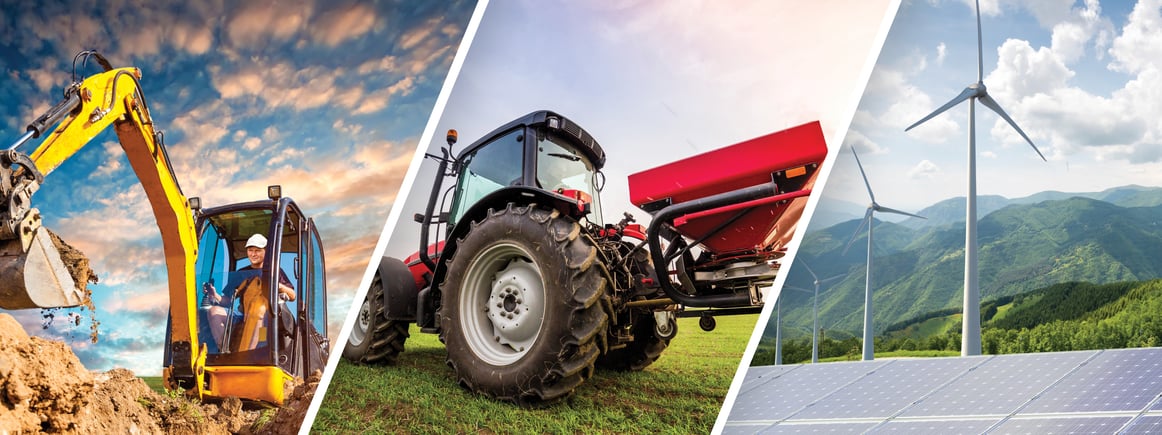
Construction
The construction industry is steadily seeing a shift toward electrification due to an increased need for efficiency, zero emission mandates and environmental safety initiatives. Larger construction and off highway equipment need high voltage systems to better manage efficiency transfers/gains and also allow systems to charge much faster. Electric construction equipment powered by Li-ion batteries will soon be the industry standard in vehicles as varied as demolition equipment, telehandlers, boom lifts, excavators, skid steers and compact loaders.
It is predicted that by 2025 or 2026, the industry will have largely shifted over from 48V battery systems up to 400 volts . With a range of 30 to 100 horsepower converting electric, this is a marked increase from today’s standards. The energy sweet spot for most construction equipment ranges between 20kWh to 80kWh for managing an 8 hour working shift on a single charge. Additionally, other elements that contribute to higher efficiency systems include the power train (motor controller) and how it is charging (i.e. DC fast charging). The goal in off-highway and construction equipment is to support fast charging between 30kW-250kW systems where equipment can charge from 20-80% in 20 minutes. In order to ensure the successful electrification of this industry, a high voltage charging infrastructure needs to be developed, such as portable charging stations on construction sites for overnight charging or opportunity charging.
Forestry & Agriculture
Vehicles dedicated to agricultural use include tractors and backhoes, which can weigh up to three to five tons. Vehicles in this group have extremely heavy carrying capacities, which can be a lot for batteries to handle, but high-voltage batteries help ensure they manage this safely and efficiently.
Large tractors are transitioning to high voltage systems ranging from 80 to 100+ horsepower. Major OEMs are starting to announce plans to electrify their agriculture equipment using Li-ion technology or hydrogen power, but the limiting factor is infrastructure.
Off-Grid Energy Storage
Off-grid energy systems (typically 1000-1200 volts) are designed to work on their own and rely on alternative renewable energy sources such as the sun and wind. The most common example of this would be solar panels, which then provide power to the battery. These batteries allow the user to rely solely on the power obtained from the sun and to disconnect from a utility provider.
Greater Demands, Greater Complexity
The unique complexities of high voltage battery design can translate into improved performance and safety with consideration of several key factors. Higher safety requirements are needed because of voltage arcs. Proper equipment for manufacturing is required for protection and isolation. Different system components also need protection and isolation from voltage arcing to eliminate failure. Redundancy in safety protections should be implemented on mechanical, electrical, and software implementation. If there is a failure, it needs to fail safely.
From a design perspective, there are also higher standards. At Inventus Power, we design, test and certify our high voltage products to SAE standards for shock & vibration, UL for on and off-road safety and ISO 26262 for functional safety. Other regulatory needs, specifically in Europe, include ECE R100 certification which is a requirement for any homologated vehicle on the road, both low and high voltage battery systems.
Inventus Power’s Path to High Voltage
Inventus Power started developing and manufacturing our standard platform of low voltage systems with the launch of our PROformance Series Batteries for Light Electric Vehicle (LEV) applications. Leveraging our 60+ years of battery industry expertise and the learnings from our customers that we’ve helped transition to Li-ion electric power, we have increased our understanding of motive power system needs and design requirements. Our highly modular and scalable architecture will help support new customers transition to high voltage technology.
Ready to discuss your high voltage power application needs? Contact us today to start a conversation.