Along with receiving supplier recognition and performance awards from some key OEM customers, Inventus Power's Qingxi, China (QX) factory has been working to improve operations by utilizing a Lean Six Sigma (LSS) methodology. Amy Zhang, Lean Sr. Engineer at Inventus Power, shares some of the recent updates made at our QX factory through the efforts of our employees and their commitment to lean.
Journey to Lean
The Inventus Power QX factory started its Lean Journey with the support of a strategic OEM customer within the commercial mobile computing industry. Lean Six Sigma (LSS) training along with transformation workshops were conducted to identify opportunities for improvement and create an implementation plan based on the LSS requirements. Since then, QX employees are continually being trained on lean manufacturing principles and developing implementation strategies for other key customers. Value Stream Mapping, Takt time, Spaghetti diagrams, Cell line design, IE seven methods, DMAIC are some tactics used by Inventus Power QX in its quality, cost, delivery, and safety improvement activities.
Highlighted below are some of the LSS initiatives recently conducted at our QX facility:
• Cell line design to support manufacturing mix of high/low volume products
• GTM and mix mode line analysis to reduce change over time
• Spaghetti diagram mapping analysis to minimize transfer distance
• OBC & OMS analysis to improve productivity
• Implementation of POU system to optimize online inventory
• Andon system and layered meetings to quicken response time and reduce downtime
• SMT smart workshop – use MES system to verify material, record downtime and FPY data systematically and automatically
• Potential risk identification in advance via micro process mapping and PFMEA and take action proactively
• Quality risk reduction by error-proofing from DFX, automatic equipment, and test station interlock
Continuous Improvement
The QX facility continues to conduct employee training on LSS system requirements. The basic training covers all production employees, which enables the front-line operators to clearly differentiate the value-added from non-value-added activities, helping them actively find the eight wastes in the work and raise up suggestions for improvement.
A Continuous Improvement Committee and recognition guidelines encourage all employees to suggest improvement ideas in their daily work. Monthly recognition ceremonies are held to motivate all employees to proactively join the improvement activities. The QX factory receives about 20 CIP projects every month from employees.
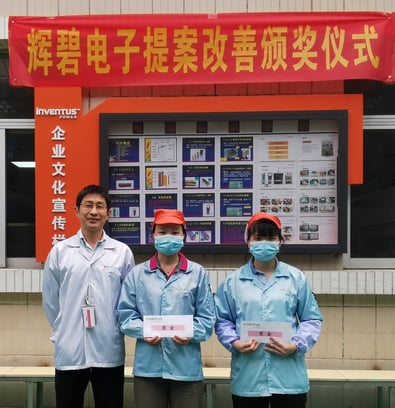
Endless Pursuit of Customer Satisfaction
Today's market is very competitive and we must ensure we are meeting, if not exceeding our customer's expectations. One method for helping us achieve this critical business objective is through Lean Six Sigma. LSS has helped our business eliminate waste, reduce operation costs, improve production efficiency, and enhance our manufacturing capability.
In the spirit of continuous improvement, the LSS initiative is not considered a one-time event, but an ongoing journey. During this past June, Black Belt and Green Belt training started to be arranged for employees to further promote the Lean Six Sigma system and equip teams with proven tools and knowledge to solve problems more systematically. There will be ten LSS projects this year from key customers implemented at our Inventus Power QX Factory. With the proactive involvement from all employees in LSS improvement activities, we aim to make improvements in quality, cost, OTD, and safety. By doing so, we hope to expand Inventus Power's manufacturing capabilities and market competitiveness.
Customer recognition, improved satisfaction, and continuous improvement in KPI metrics at our QX factory is a goal that we set to achieve through the hard work of all cross-functional teams and from the journey of Lean Six Sigma. We believe that Inventus Power will have a brighter future as a result of our continued LSS initiatives in QX as well as our other global manufacturing locations.